"The cement sector in Bangladesh transcends its role as a mere producer of construction materials; it stands as a foundational force propelling the nation's development, exerting a pivotal influence on its infrastructure, economy, and overall advancement."
As per the Bangladesh Cement Manufacturers Association (BCMA), the annual sales of the country's cement industry were approximated at USD 3 billion in 2020, positioning Bangladesh as the 20th largest cement market globally, underscoring its significance on the international stage.
Although Bangladesh maintains self-sufficiency in cement production, it actively participates in exports, garnering USD 8.06 million in export revenue during the initial nine months of the fiscal year 2019-20. Projections for the global cement market forecast growth from USD 340.61 billion in 2022 to USD 481.73 billion by 2029, indicating a compound annual growth rate (CAGR) of 5.1%.
In light of this worldwide trajectory and Bangladesh's continuous infrastructural development, the domestic cement industry anticipates sustained expansion in the foreseeable future. However, this growth entails an increased reliance on Imported Clinker, the primary raw material for cement, rendering Bangladesh susceptible to the ongoing foreign exchange fluctuations in the economy.
Imported clinker arrives at the cement plant in bulk or bagged form. The clinker is then finely ground, typically using ball mills similar to those used for raw materials in traditional cement production. Gypsum, acting as a setting time regulator, is also finely ground. Precisely measured proportions of the ground clinker and gypsum are then blended together to create a homogeneous cement mix. Some manufacturers may also add supplementary materials to the blend at this stage, depending on the desired properties of the final cement. These materials could include fly ash, slag, or silica sand. Each material undergoes its own grinding process if necessary before being incorporated into the mix.
The Bangladeshi cement industry relies significantly on the importation of clinker, a crucial component in cement manufacturing. Despite the nation's self-sufficiency in cement production, the shortage of domestic sources for essential raw materials, particularly limestone needed for clinker production, poses a challenge. Bangladesh annually imports approximately 10-15 million metric tons of clinker, constituting a substantial portion of its overall clinker demand.
A news report from "The Business Standard" in October 2023 revealed that in the fiscal year 2021-2022, Bangladesh imported 2,328.17 crore tonnes of clinker valued at Tk13,407 crore, equivalent to an estimated cost of USD 1.63 billion based on the average exchange rate during that period.
The domestic production of clinker is limited, with only two local manufacturers, notably Lafarge Surma Cement, contributing about 10% of the total demand. Import sources for clinker primarily include countries such as Vietnam, Thailand, Malaysia, and Indonesia, while China, once a major supplier, scaled back its contributions due to tightened regulations on clinker production prompted by environmental concerns.
Reasons for Clinker Dependence:
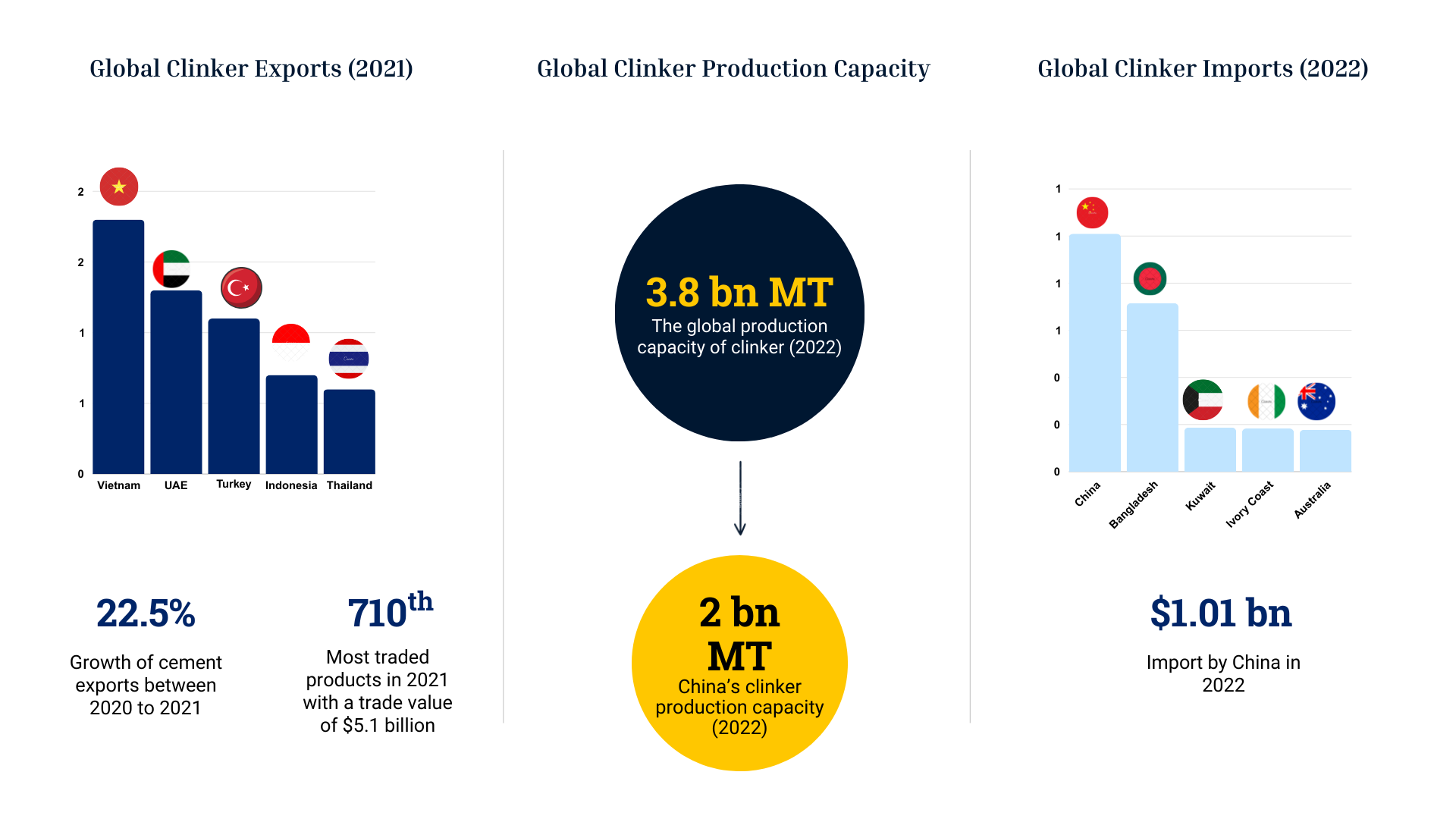
Lack of Limestone Reserves: Bangladesh has limited high-quality limestone reserves suitable for clinker production. Most available limestone deposits are unsuitable due to their chemical composition or location.
Cost-Effectiveness: Importing clinker can sometimes be cheaper than setting up and operating domestic clinker plants, especially considering the high energy consumption involved in clinker production.
FLOW
One Platform, Endless Efficiency.
Create automations to increase efficiency and smoothen workflow.
Try Now!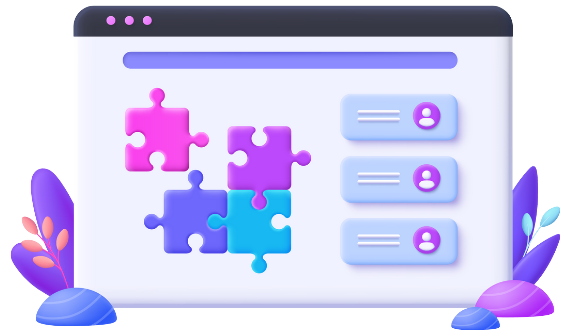
Sustainable Alternatives
Manufacturers are exploring the use of alternative materials like fly ash and slag in blended cements, lowering clinker content and carbon footprint, such as
1. Supplementary Cementitious Materials (SCMs):
These materials, when used in conjunction with clinker, offer similar binding properties. Some common SCMs include:
- Fly ash: A byproduct of coal-fired power plants, fly ash can replace up to 50% of clinker in blended cements, reducing CO2 emissions and energy consumption.
- Ground blast furnace slag (GBFS): A waste product from steelmaking, GBFS can also contribute up to 50% clinker replacement, improving strength and durability of concrete.
Ground blast furnace slag for cement production - Silica fume: A very fine pozzolanic material made from silicon metal production, silica fume can improve strength, durability, and resistance to chemicals in concrete, but typically used in smaller proportions due to its cost.
Cost Comparison: SCMs are generally cheaper than clinker, making them economically attractive, especially when blended in significant proportions. For instance, fly ash, a readily available waste material, can significantly reduce production costs.
2. Calcined clays: These clays are treated with heat to enhance their pozzolanic activity, allowing them to contribute to the cementitious properties of blended cements. While not as widely used as fly ash or slag, calcined clays can be a viable option in regions with limited access to other SCMs.
Cost Comparison: The cost of calcined clays can vary depending on processing and transportation costs, but it generally falls between clinker and fly ash.
3. Geopolymers: These novel binders are based on aluminosilicate materials and activated by an alkaline solution. While still under development, geopolymers have the potential to offer significant environmental benefits compared to traditional clinker-based cement.
Cost Comparison: Currently, geopolymer technology is less mature and the cost can be higher than conventional cement due to limited production and higher activation material costs. However, ongoing research and development efforts are aiming to make geopolymers more cost-competitive in the future.
WHY The High Dependency?
So one might ask, if alternatives to clinker exist then why the high dependency? The reasons why clinker remains the dominant ingredient in cement production today are briefly described below:
Technical Requirements: Clinker forms the backbone of traditional portland cement, providing essential strength, durability, and setting time properties. Some applications like high-performance concrete or infrastructure projects with specific load-bearing requirements might need the superior properties offered by traditional clinker-based cement.
Established Infrastructure: The current cement manufacturing infrastructure is largely geared towards clinker-based production. Investing in significant upgrades or entirely new facilities for alternative materials can be cost-prohibitive for manufacturers, delaying widespread adoption.
Lack of Awareness and Knowledge: Lack of awareness or expertise among some manufacturers can create a barrier to adoption.
Regulatory Hurdles: In some regions, regulations and standards for blended cements using alternatives might be less established or more stringent than those for traditional clinker-based cement. This can create uncertainty and discourage wider adoption.
Cost Considerations: While certain alternatives like fly ash might be cheaper than clinker, other options like calcined clays or geopolymers can be more expensive due to processing cost or limited availability. Manufacturers need to balance cost-effectiveness with desired performance parameters, potentially favoring clinker in some scenarios.
Conclusion
However, it's important to recognize that the tide is turning. Growing environmental concerns, regulations and technological advancements are pushing the industry towards adopting cleaner technologies and reducing clinker content in cement. In conclusion, while clinker continues to be the main ingredient in cement production today, the landscape is changing. With continued research, development, and supportive policies, clinker alternatives have the potential to become the mainstay of a more sustainable future for the construction industry.