‘Building smarter, not harder: Prefabrication and modular construction offer a promising path, promising quicker build times, improved quality, and cost-effectiveness for a more sustainable and resilient future’
Bangladesh, a nation known for its resilience and dynamism, is facing a growing demand for housing and infrastructure. Traditional construction methods, however, struggle to keep pace with this demand, hampered by factors like skilled labor shortages, lengthy project timelines, and environmental concerns. In this context, prefabrication and modular construction are emerging as game-changers, offering the potential to revolutionize the Bangladeshi built environment.
Prefabrication in Bangladesh
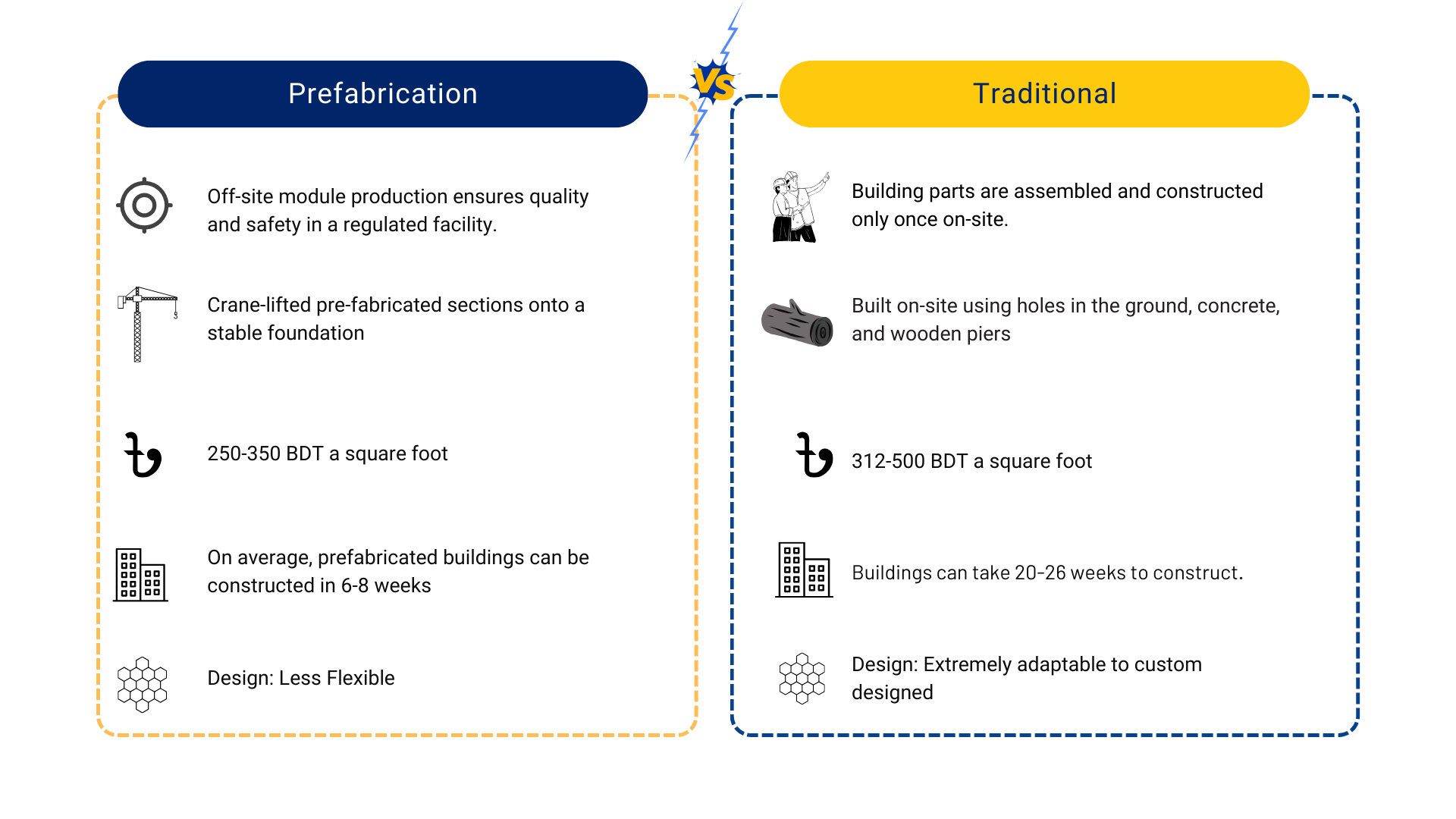
Prefabrication in Bangladesh
Prefabrication is the process of constructing a building's components inside a factory in accordance with the blueprint, then moving those components to the construction site and connecting them to create the building. Prefabricated buildings are a relatively new concept.
Prefabrication offers a real benefit to improve the sustainable behavior and performance of projects. Bangladesh's construction sector is attempting to use modern building methods to build structures that are efficient and sustainable. Prefabrication could prove to be an astute approach in this scenario, as it can amalgamate every conceivable benefit to enhance construction methodologies.
Price: $45 to $100 per square meter
Modular Construction in Bangladesh
Modular construction is a form of prefabricated construction wherein separate building components or modules are manufactured off-site. After that, these modules are delivered to the construction site and put together. Like prefabrication, modular building has the advantages of shorter construction schedules, lower costs, and better-quality assurance.
Price: $5 to $ 35 per square foot
Construction time
Prefab House: Four to seven days are needed for manufacturers to construct a prefabricated house at their factories. Four months after placing an order with their builder, new homeowners can move into their freshly delivered home.
Modular House: A modular home typically requires three to four months to complete. The foundation and the house can be constructed at the same time, which is one of the reasons for the shorter building period.
Prefabricated Builders in Bangladesh
Residential: DTH Prefab, Karmod, ShelterTech.
Commercial and Industrial: ALM Steel Building Technology Ltd, Unibond Engineering & Technologies.
Public: Karmod, UNICEF, BRAC.
Temporary: DTH Prefab, ShelterTech
FLOW
One Platform, Endless Efficiency.
Create automations to increase efficiency and smoothen workflow.
Try Now!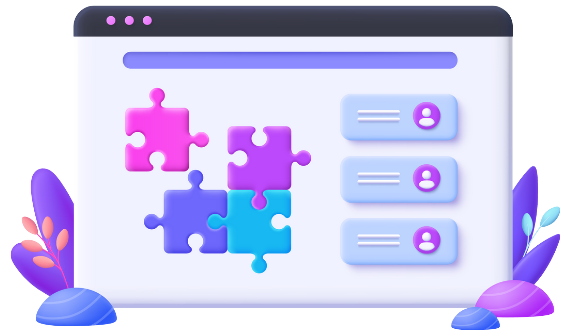
Market Landscape
The prefabricated construction industry in Bangladesh is expected to grow by 14.9% to reach BDT 46 billion in 2023, according to the data book published by Market Research. The growth momentum is expected to continue over the forecast period, recording a CAGR of 13.7% during 2023-2027. The prefabricated construction output in the country is expected to reach BDT 77 billion by 2027.
The medium to long-term growth story in Bangladesh remains intact. The prefabricated construction industry in Bangladesh is expected to grow steadily over the next four quarters. The growth of the market will be supported by investment in rail, electricity, industrial, and telecommunication infrastructure projects.
According to the analysis of Mordor Intelligence, the overall construction market in Bangladesh was estimated at USD 32.33 billion in 2024 and is expected to reach USD 44.13 billion by 2029, growing at a CAGR of 6.42% during the forecast period (2024-2029). The prefabricated and modular construction methods are gaining popularity and are expected to claim a significant share of this market.
Sustainable Construction
Prefabrication often utilizes prefabricated and recycled materials, minimizes construction waste, and reduces on-site energy consumption. This aligns with Bangladesh's growing focus on sustainable development.
i. Recycled Wood: It’s environmentally friendly and helps reduce waste.
ii. Clay: It’s durable, recyclable, and has excellent thermal properties.
iii. Mass Timber: This includes products like Cross-Laminated Timber (CLT), which is a strong, prefabricated wood panel made by layering and gluing several layers of lumber together. CLT is a renewable resource with a lower carbon footprint than traditional building materials like steel and concrete.
iv. Concrete: Recycled concrete can be used in the construction of prefabricated buildings.
v. Steel: Recycled steel is another material that’s often used in prefabricated buildings.
vi. Glass: Recycled glass can be used in the construction of prefabricated buildings. It’s versatile and helps reduce waste.
vii. Plastics: Non-virgin plastics can be used in the construction of prefabricated buildings.
viii. Salvaged Building Components: These are parts of buildings that have been dismantled and can be reused in new construction.
Challenges
While prefabricated buildings offer many advantages, they also come with a few disadvantages:
i. Limited Design Options: Compared to traditional building methods, prefabricated construction may offer limited design options.
ii. Transportation and Storage Challenges: The transportation and storage of the pre-built components can be challenging due to their size and weight.
iii. Handling and Breakages: Handling and transportation may cause breakages of members, so care has to be taken.
iv. High Transport Cost: The cost of transporting the prefabricated components from the factory to the construction site can be high.
v. Need for Specialized Equipment and Skilled Labor: Prefabricated construction requires specialized equipment for installation and skilled labor for assembly.
vi. Non-Monolithic Construction: Prefabricated buildings are non-monolithic, meaning they are made up of separate units or modules. This can lead to a different aesthetic or feel compared to traditional construction.
Future Potential of Prefabrication
With its inherent advantages and increasing government support, prefabrication and modular construction are poised to play a significant role in shaping Bangladesh's future. By addressing existing challenges and promoting collaboration among stakeholders, Bangladesh can harness the power of these innovative methods to build a more sustainable, resilient, and inclusive built environment for its citizens.